レーザー微細加工とは?
レーザー微細加工(Laser micromachining)とは、レーザーを用いて微細な加工を行うことです。
『微細』の定義はさまざまあると思いますが、ここでは、概ねフィーチャーサイズが0.1mm以下のものを指します。『微細』は、正確には『精密』とは意味が異なります。『精密』とは、真の値からのずれ(ばらつき)が小さいことを指します。しかし、程度によりますが、精密に加工ができなければ、微細な加工にはならないので、この『精密』な加工も含めて『微細加工』と称することにします。
レーザー以外の加工方法でも、微細加工は可能です。世の中には、φ0.01mmのドリルも市販されており、実際の加工例もあります。半導体製造で用いられる装置では、レーザーで直接加工できないようなナノメートル(nm)オーダーの超微細加工が実現されています。
しかし、どの加工方法にも得手不得手があり、目的に応じて加工方法は適切に選択する必要があります。機械加工で微細加工を行うためには、相当なスキルと開発投資が必要でしょう。半導体装置に至っては、膨大な投資金額がかかります。
レーザーにより微細加工は、導入のしやすさ、装置の扱いやすさ、得られる結果・効果の大きさ、からすると、非常にメリットが大きい加工方法だと思います。
レーザー微細加工の特長
レーザーの特長を最大限に活用すると、除去加工において次のような特性を得ることができます。
・微細:レーザーを微小な点に集光して加工を行うため、微細なフィーチャーを創成できます。
・精密:レーザー加工は、再現性の良い加工であるため、安定した品質を実現できます。
・フレキシブル:オンデマンド加工のため、任意の時に任意の形状ですぐに結果が得られます。
・低熱影響:通常のレーザー加工と異なり、極々短時間で加工を完結できるため、熱による悪影響がないです。
・クリーン:環境を汚す材料や溶剤等を使用せずクリーンな状態で加工できます。
以下の写真のように非常に小さくて精密な加工をレーザーにて実現できます。ドロスやバリの発生はほとんどありません。微細で高品質な加工をレーザーで行うことが、『レーザー微細加工』です。
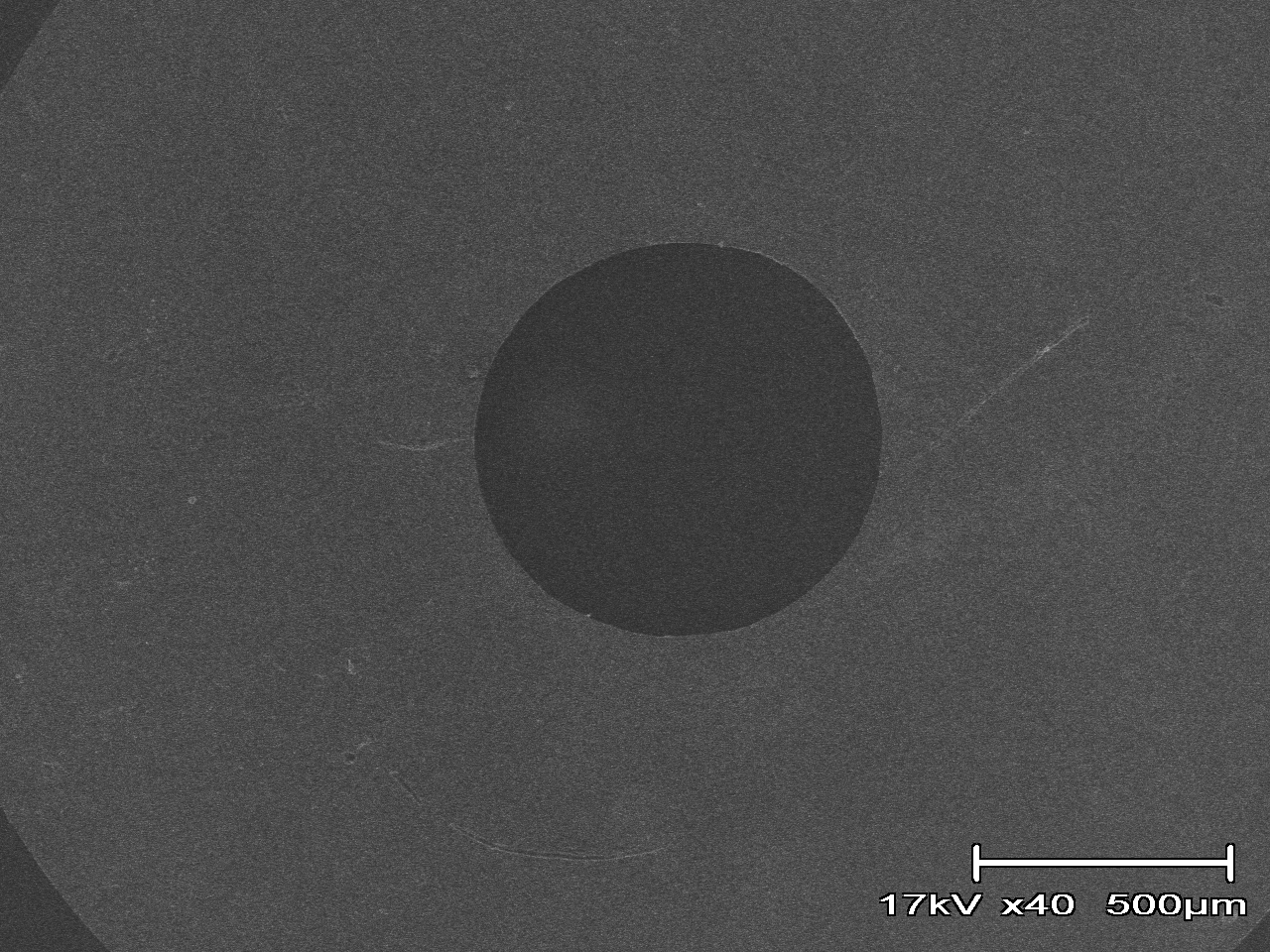
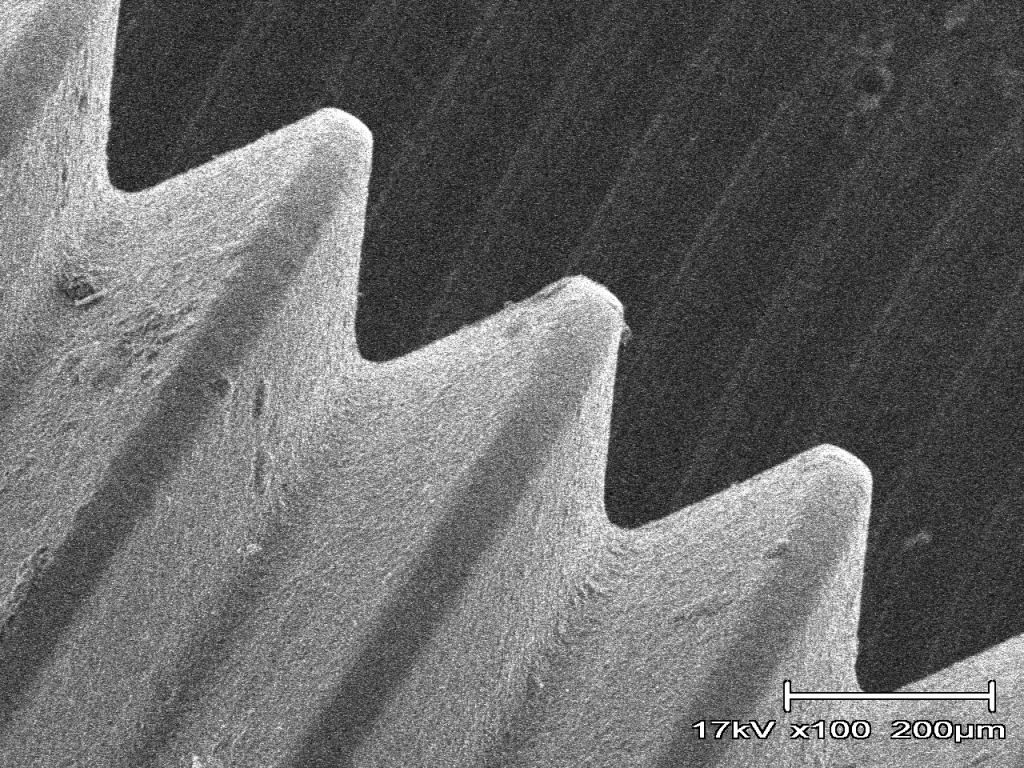
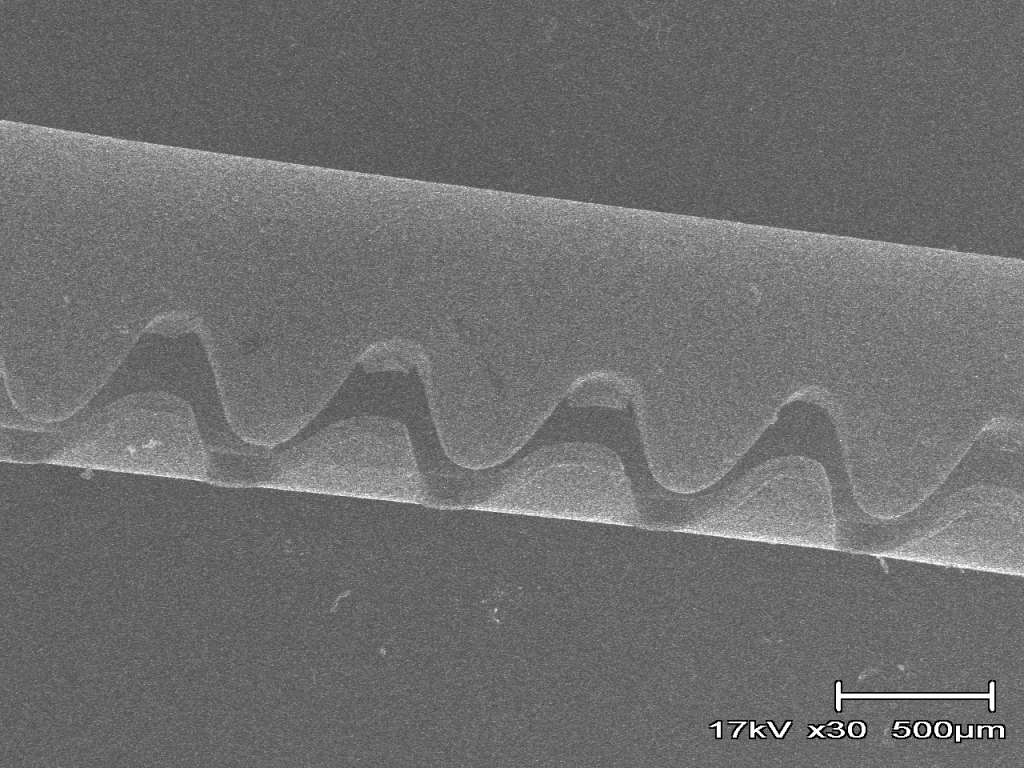
レーザー微細加工の実際
レーザー加工でもっとも重要な箇所は、刃物にあたるレーザー光源です。この光源の選定、使用方法により結果に大きな違いが出てきます。
レーザー光源は、フェムト秒レーザー、ピコ秒レーザーのようなパルス発振の超短パルスレーザーを用いることがほとんどです。フェムト(10-15)、ピコ(10-12)秒という非常に短い時間だけレーザーを照射できる特殊なパルスレーザー光源を使用します。1つのパルスでの物質の除去量はわずかですが、このパルスを非常に高い周波数で繰り返し照射し、加工することで、単位時間当たり大きな加工をすることが可能です。
さらに、短い間隔で繰り返し加工を行う「バーストモード」という機能を備えたレーザーもあります。バーストモードの各パルスをより精密に制御できるようになっているレーザーもあり、多機能化が進んでいます。
また、近年は、加工用の大出力パルスレーザーも多く市販されており、ますますその活躍の場が広がっています。
近年のパルスレーザー加工の特徴は、以下のようになっています。
- 短パルス化:より短いパルスを用いた加工になっています。
- 短波長化:より波長の短いレーザーを用いるようになっています。
- 高出力化:加工効率を上げるために、レーザーの大出力化が進んでいます。
一方、レーザー以外の機構も重要です。
正確に微細な加工を行うには、加工する刃物に相当するビームスポットを正確に移動させる必要があります。通常ビームの走査は、2枚のミラーを用いるガルバのスキャナーや精密ステージを用います。
ガルバノスキャナーでは、高速な走査が可能です。最近は、デジタルタイプも増えてきており、高速に正確にスキャンができるようになっています。
精密ステージは、サンプルをXY平面(及びZ軸)で正確に移動させます。エンコーダーや干渉計でその位置を正確に測定して制御します。
さらに、レーザーを光源から加工点まで安定的に伝搬させる必要があります。そのために、レーザーの伝搬経路を窒素パージされたチューブの中に限定したり、レンズの反射防止コートはもちろん、光学部品を安定的に固定する機構もあります。
また、装置全体の振動や温度変化による加工誤差の影響を低減させるため、光学機器等は石定盤の上に固定され、除振装置で支持されることが多いです。除振の方法も、受動的(パッシブ)や能動的(アクティブ)など目的や予算に合わせて選定します。
レーザー微細加工の未来
レーザー微細加工は、非常に難しい加工技術です。様々な加工パラメータが複雑に絡み合い、材料そのものや外乱によっても加工結果に影響があります。
一方で、既存の加工技術では、困難であった加工を、比較的容易に行えることが大きなアドバンテージです。
つまり、レーザーのもつメリットを最大限に利用できる技術といえます。
今後ますますの飛躍が期待されます。